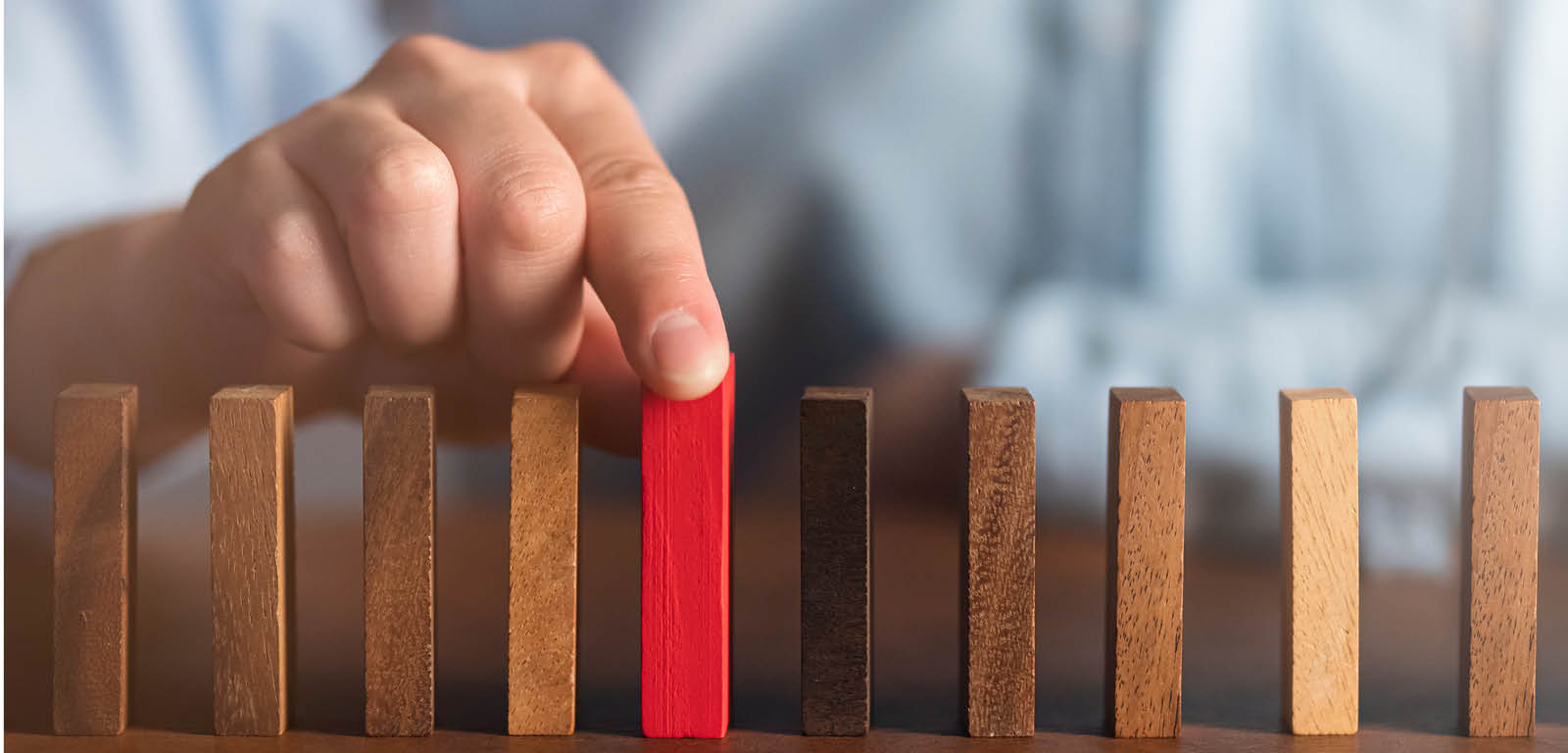
The disruption of the global supply chain continues to impact the home textile and bedding industry. Manufacturers of pillows, quilts, and mattresses are forced to adopt new and innovative strategies to remain competitive, which in turn is becoming an opportunity for them to innovate and build a more resilient system that can withstand future uncertainties.
We are about to explore the latest trends for the upcoming years, offering insights into reshoring, nearshoring, supply chain challenges, automation, integrated software and the growing importance of sustainability.
UNDERSTANDING SUPPLY CHAIN DISRUPTION
Let’s start with the facts: the global supply chain disruption of 2023, fueled by the COVID-19 pandemic and geopolitical tensions, has created delays, lack of materials and bottlenecks at ports. As a result, manufacturers face challenges such as labor shortages, rising shipping costs, and the need to reduce reliance on certain regions.
With its long history of spanning production processes all over the world, the textile industry has been severely impacted by current events, forcing businesses to rethink traditional manufacturing by taking a closer look at their supply chain strategies.
As a result, many companies have shifted to more localized production, reducing their reliance on overseas manufacturing. Technology in the supply chain has also taken center stage: businesses are investing in digital tools such as predictive analytics and blockchain to improve visibility and traceability.
BRINGING MANUFACTURING HOME
Many home textile and pillow manufacturing companies are bringing their operation back to their home countries in order to create a more stable supply chain and boost the local economy. The benefits of this movement, also known as reshoring, are endless – reduced transportation costs, shorter lead time, enhanced quality control and local job creation. The US and EU have especially experienced a surge in reshoring as companies realize the advantages of this approach.
Since 2010, the US non-profit organization Reshoring Initiative has been tracking data and trends of companies who are shifting production from offshore back home. According to their reports, between 2010 and 2018, approximately 749,000 jobs were brought back to the US while 2022 reported a significant spike with 220,000 new jobs created in the US alone.
But it’s not just reshoring: nearshoring is also taking hold, meaning companies are bringing back manufacturing not in their own home country but in nearby location. In the EU, according to the Interred Europe, countries like Sweden, Denmark, Italy, France, and Portugal are becoming attractive locations for reshoring and nearshoring textile manufacturing activities due to their greater cost advantages and their opportunities in terms of raw material inputs, intermediate goods production, and joint development.
AUTOMATION AS A SOLUTION FOR LABOR SHORTAGES
To address the recent logistics challenges, and especially the shipping delays and the significant hike in shipping costs, businesses are increasingly turning to automation to streamline operations and enhance efficiency. By implementing automated production lines equipped with cutting-edge machinery and integrated software, these companies are reducing their reliance on manual labor and optimizing output, thereby ensuring timely delivery despite external disruptions.
Another reason why businesses are turning to automation is labor shortages, especially of skilled workers: to address this issue, highly automated manufacturing processes are projected to surge from 18% in 2021 to 47% in 2024. In particular, the integration of software in manufacturing operations creates an interconnected environment which can be easily monitored and managed in real-time facilitating quicker decision-making and the ability to adapt to market fluctuations promptly.
INTEGRATED SOFTWARE TO SOLVE LOGISTIC CHALLENGES
In 2024 automated machines won’t cut it: businesses need other tools such as software, AI, machine learning, and cloud computing to thrive in the market. With these digital solutions, businesses are able to build more intelligent networks and obtain more accurate demand forecasting, ensuring they are always well-prepared.
That’s because creating a digitalized environment can help businesses in every step of the process: from raw material sourcing to optimizing production flow, maintenance schedules, supplier interactions, and beyond. By harnessing the power of digital technologies and software solutions, companies can achieve greater visibility, efficiency, and agility across their entire manufacturing ecosystem.
With the right technologies, these data can also be automatically shared with suppliers and distributors to identify potential issues early on and work together to find solutions. Improving collaboration and communication with the stakeholders is another important piece to keep the supply chain running smoothly. Integrated software solutions provide real-time visibility into inventory levels, demand forecasts, and production schedules, empowering manufacturers to make informed decisions and adapt swiftly to changing market dynamics.
Despite the countless advantages, the heightened use of advanced technologies elevates cybersecurity concerns, given the interconnected nature of intelligent networks, cloud computing, and automated systems. Businesses must prioritize cybersecurity measures, collaborating with industry stakeholders to establish standardized protocols and fortify their systems against potential disruptions.
MEETING THE NEEDS OF THE MODERN CONSUMER: PERSONALIZATION AND ENGAGEMENT
Last but not least, manufacturers cannot forget about their customers and their expectation. The latest emphasis is on locally made and sustainable options. In the United States, this trend has also clearly emerged from a survey, where a substantial 70% of respondents expressed a preference for domestically manufactured goods—a reflection of the ongoing reshoring initiatives.
For pillow manufacturers, for example, meeting these demands necessitates added flexibility in product range, which can only be possible if supported by the right technologies.
This versatility allows manufacturers to cater to various sectors such as ho.re.ca, work with renowned brands, or even establish their own. Choosing the right equipment which can process a wide range of materials, including fibers and other filling materials, allows them to adapt swiftly to changing market trends and consumer preferences. By integrating advanced technologies into their production processes, pillow manufacturers can enhance efficiency, reduce costs, and ultimately meet the evolving demands of the market while maintaining high-quality standards.
WHAT BRIGHI BRINGS TO THE TABLE
“Studying where the industry is going is giving us a head’s up on the technology needed to support manufacturers and their growth”, says Matteo Brighi, COO at Brighi.
“As businesses navigate difficulties and relocate their production facilities, they will need a knowledgeable partner to help them set up their manufacturing operation. For years we have been developing technologies to support businesses and help reduce costs where it matters most, at the beginning and the end of the production line. Whether it is machines to optimize raw material usage or technology to reduce packages’ volume for shipping, our production lines support manufacturers every step of the way. But it is not just machines: it’s a partner that always ensures excellent technical support, along with digital solutions, to predict, control and assess the entire process.”
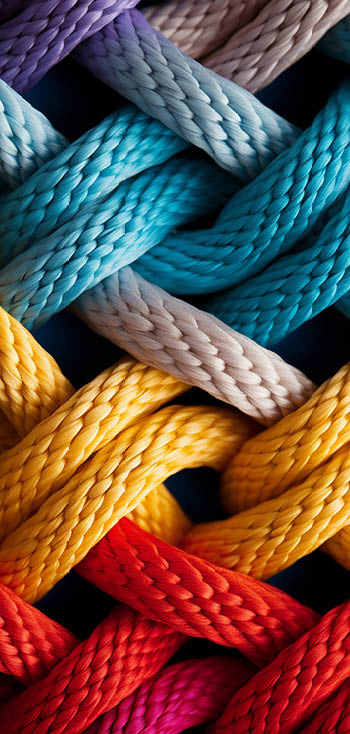